5 Simple Techniques For Alcast Company
Table of ContentsThe Definitive Guide for Alcast CompanyHow Alcast Company can Save You Time, Stress, and Money.Some Of Alcast CompanyThe smart Trick of Alcast Company That Nobody is Talking AboutAlcast Company for BeginnersAbout Alcast CompanyAlcast Company Fundamentals Explained3 Simple Techniques For Alcast Company
It had great toughness and machinability. There are numerous various other light weight aluminum alloys that can be used for casting parts. To discover out which alloys would be excellent for your jobs, call Impro.
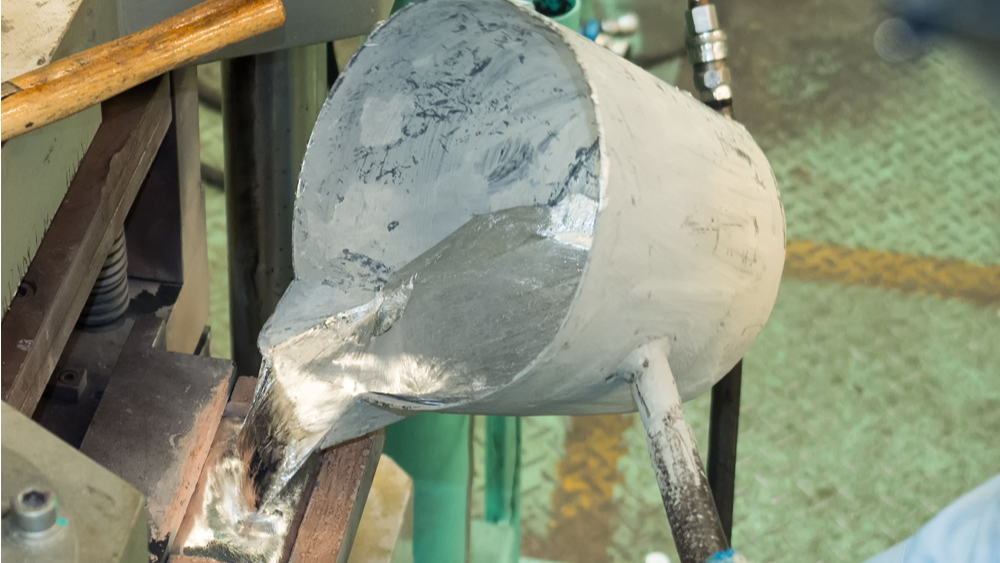
(AA), based in North America, has produced specifications that control aluminum alloys' composition, residential properties, and nomenclature. There are 2 kinds of light weight aluminum alloys functioned and cast.
Get This Report about Alcast Company
Cast light weight aluminum alloys are made by thawing pure aluminum and incorporating it with various other metals while in fluid form. The mix is put into a sand, die, or investment mold.
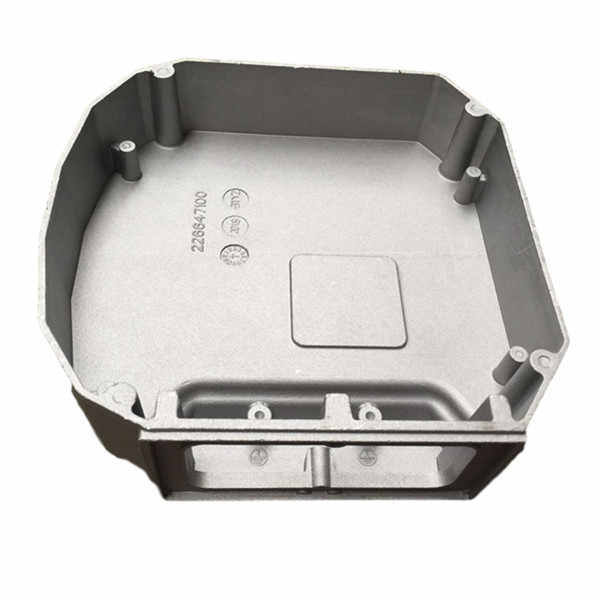
There are many minor differences in between functioned and cast aluminum alloys, such as that actors alloys can have much more significant amounts of other metals than wrought alloys. The most notable difference in between these alloys is the fabrication process via which they will certainly go to supply the last item. Other than some surface area therapies, cast alloys will certainly exit their mold in nearly the precise solid type wanted, whereas functioned alloys will certainly undertake several adjustments while in their solid state
6 Simple Techniques For Alcast Company
If you think that a wrought alloy may be the best for your job, take a look at some of our posts that explain even more about certain wrought alloys, such as Alloy 6061 and Alloy 6063. On the various other hand, if you assume a cast alloy would be much better for you, you can find out more about some cast alloys in our Alloy 380 and Alloy 383 short articles (coming soon).
When selecting an aluminum foundry for your production needs, it's important to study several aspects. Among the most essential aspects to consider is the experience and capability of the foundry. Choosing a shop who has the appropriate expertise of the light weight aluminum spreading process, and the profile to show for it, helps to have an effective end result for your job.
The Alcast Company PDFs
Having the experience and industry expertise to engineer your castings for optimum production and quality results will certainly streamline the job. Making light weight aluminum castings calls for a complex set of procedures to attain the appropriate results. When choosing a brand-new light weight aluminum foundry to partner with, ensure they have comprehensive market experience and are educated concerning all aspects of the aluminum casting process: style, manufacturing, product evaluation, and item testing.
The foundry should also have a tested track document of supplying extraordinary products that satisfy or go beyond consumer assumptions. Quality control must also be at the top of your list when picking a light weight aluminum shop. By functioning with a certified shop that complies with the requirements for high quality control, you can safeguard the stability of your product and ensure it fulfills your requirements.
What Does Alcast Company Mean?
By selecting a firm who offers services that fulfill or exceed your item requirements, you can be certain that your project will certainly be finished with the utmost precision and performance. Different parts need various manufacturing strategies to cast light weight aluminum, such as sand casting or die casting.
Die casting is the name offered to the process of producing intricate steel parts with use of mold and mildews of the part, additionally referred to as dies. The process uses non-ferrous metals which do not consist of iron, such as light weight aluminum, zinc and magnesium, because of the preferable homes of the steels such as low weight, higher conductivity, non-magnetic conductivity and resistance to rust.
Pass away spreading manufacturing is quickly, making high manufacturing degrees of parts very easy. It produces more components than any type of other process, with a high level of precision and repeatability. To find out more regarding die spreading and pass away spreading products utilized while doing so, read on. look these up There are three sub-processes that fall under the classification of die casting: gravity die casting (or irreversible mold and mildew spreading), low-pressure die spreading and high-pressure die spreading.
More About Alcast Company
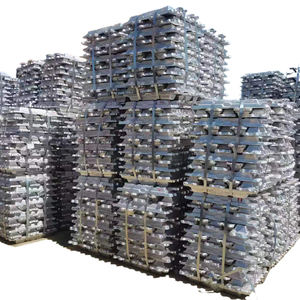
The pure steel, likewise understood as ingot, is included to the heating system and maintained at the molten temperature level of the metal, which is then moved to the shot chamber and infused right into the die. The stress is then preserved as the metal solidifies. When the metal strengthens, the cooling process starts.
The thicker the wall of the component, the longer the cooling time since of the amount of indoor metal that also needs to cool down. After the component is totally cooled, the die cuts in half open and an ejection mechanism presses the component out. Adhering to the ejection, the die is closed for the following injection cycle.
How Alcast Company can Save You Time, Stress, and Money.
The flash is the added product that is cast during the procedure. This must be trimmed off utilizing a trim device to leave just the primary part. Deburring removes the smaller items, called burrs, after the cutting process. Lastly, the part is polished, or burnished, to provide it a smooth coating.
Today, leading makers utilize x-ray testing to see the whole inside of elements without cutting right into them. To obtain to the ended up item, there are three primary alloys made use of as die casting material to pick from: zinc, aluminum and magnesium.
Zinc is one of one of the most used alloys for die spreading because of its lower price of resources. It's also among the stronger and stable steels. Plus, it has excellent electric and thermal conductivity. Its rust resistance also permits the parts to be long-term, and it is one of the more castable alloys as a result of its lower melting point.
More About Alcast Company
As discussed, this alloy is just one of the most frequently made use of, yet manufactures will, sometimes, pick aluminum over zinc because of light weight aluminum's production advantages. Aluminum is extremely affordable and among the more flexible alloys. Light weight aluminum is used for a number of different items and sectors anything from home window frames to aerospace materials.